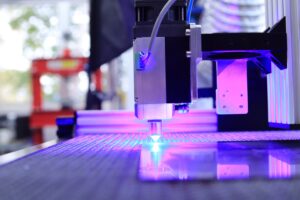
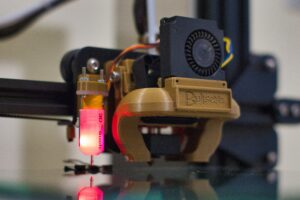


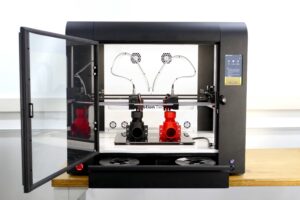
Quand on parle d’industrie 4.0 & de performance industrielle, on pense souvent aux intelligences artificielles ou aux robots collaboratifs.
Pourtant, une technologie irrigue de plus en plus l’industrie du futur, grâce à ces procédés toujours plus diversifiés et un coût de fonctionnement en constante diminution : L’impression 3D.
L'impression additive, une technologie appropriée !
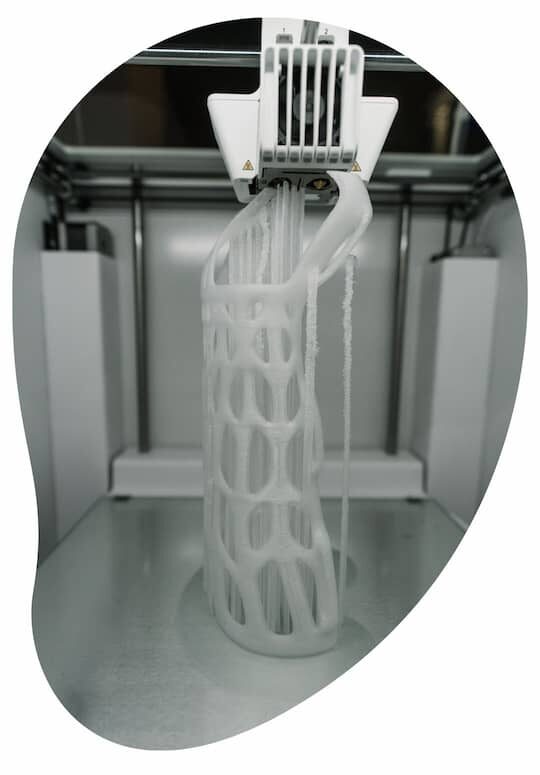
Bien que la fabrication additive ait pris un essor considérable dans les années 2010. Les imprimantes 3D, destinées au grand public, ont évoluée de « curiosité » à « procédé de fabrication mature ».
Alors que les procédés de fabrication classiques enlèvent de la matière. Les procédés de fabrication additive en ajoutent. Cette technique permet non seulement de fabriquer des pièces complexes, mais aussi de le faire sans perte de matière. Cette méthode d’impression comprend une large gamme de polymères, céramiques et métaux. Parmi eux, on retrouve le PLA, l’ABS, le TPU, le Nylon.
Le PLA, matériau le plus répandu dans la fabrication additive par dépôt de fil. Il est produit à partir de maïs, et offre l’avantage d’être un bioplastique compostable. C’est-à-dire biodégradable, mais aussi réemployable à l’infini. Les autres matériaux sont, quant à eux, des polymères classiques.
Les techniques & les coûts de la fabrication additive.
Il existe 3 grands procédés de fabrication additive, chacune apportant son lot d’avantages et d’inconvénients :
L’impression par frittage laser :
Cette technique de fabrication est réservée à l’impression métallique. Un dépôt de poudre métallique est amené en fusion par un laser selon la forme souhaitée, couche après couche.
Le prix : Pour une pièce, les prix peuvent aller de quelques centaines à plusieurs milliers d’euros suivant le paramétrage : La taille, le matériau, la finition, la complexité de la pièce rentrent notamment en compte lors du chiffrage.
L’avantage : d’un tel procédé est la possibilité de fabriquer rapidement une pièce avec précision, sans avoir recours à de nombreuses machines d’usinage. Cela permet aussi de concevoir et de fabriquer des pièces à conception multi-matière, par exemple une pièce ductile d’un côté et très dure de l’autre.
L’inconvénient : Le coût, car il est peu attractif par rapport aux méthodes d’usinage classiques.
Exemple : En prenant la fabrication d’une pièce de 1 kg, pour 10 heures de fonctionnement machine, le coût moyen de fonctionnement de ce type d’installation (matière + consommation électrique) revient à 270 euros (266 euros par kg de matière, une consommation électrique de 1,725 kWh). Comptez plus ou moins 30 000 euros pour une machine d’impression par frittage laser.
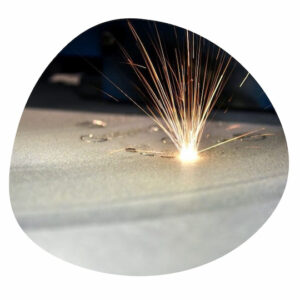
L’impression par photo-polymérisation :
Cette technique permet d’imprimer des pièces en polymère avec une très bonne précision (≈ 0,05 mm). Pour cela, un plateau est plongé dans une cuve de résine liquide qui durcit lorsqu’elle est exposée aux Ultraviolets. Les UV projetés permettent d’imprimer couche par couche des pièces complexes.
L’avantage : Principal de cette méthode est la précision d’impression, qui permet d’imprimer des pièces de petites tailles, tout en conservant une très bonne qualité de surface.
L’inconvénient : Cette technique est longue, et chaque pièce imprimée doit être nettoyée et polie après impression pour un rendu optimal. Aussi, cette technique ne permet l’impression que de pièces en résine.
Exemple : En reprenant le même que précédemment. Le coût moyen de fonctionnement de ce type d’installation (matière + consommation électrique) revient à environs 60 euros (60 euros par kg de matière, et une consommation électrique de 0,12 kWh). Le coût d’achat d’une machine neuve, lui, est d’approximativement 400 euros.
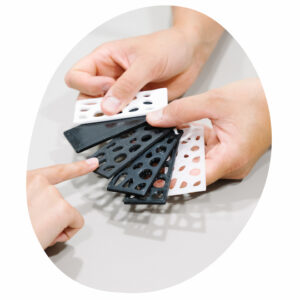
L’impression par dépôt de fil :
L’avantage : Cette technique permet d’imprimer des pièces complexes avec une bonne précision (≈ 0,05 mm), et avec un minimum de perte matière. De plus, la diversité des matériaux la rend très pertinente dans de nombreux domaines d’application. PLA, ABS, TPU, Nylon, TPE, qui sont les matériaux les plus utilisés pour ce procédé, possèdent des propriétés mécaniques intéressantes :
Conclusion : C’est avec ce procédé que les modèles proposent les spécificités les plus intéressantes (1 ou 2 buses, précision d’impression variable, plateau chauffant, etc). Cette dernière permet d’imprimer des pièces complexes en polymère par dépôt de couches. Une buse, par laquelle le fil est amené en fusion, dépose la matière sur un plateau, la forme souhaitée, couche après couche.
Exemple : Toujours avec le même exemple. Le coût moyen de fonctionnement de ce type d’installation (matière + consommation électrique) revient à environ 24 euros (24 euros par kg de matière, et une consommation électrique de 0,12 kWh). Le coût d’achat d’une machine neuve, lui, est d’approximativement 200 euros suivant les modèles.
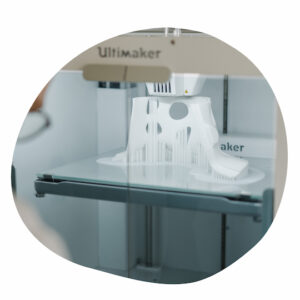
Applications de l'impression additive dans l’industrie
Les applications se diversifient à mesure que les industries adoptent ces techniques de fabrication dans leurs process.
- L’industrie aéronautique est un secteur qui fabrique des pièces de petite série. La fabrication additive est donc pertinente pour ce domaine, et permet de réduire les coûts de production et les pertes de matières.
- L’industrie navale fabrique des pièces complexes, comme des hélices. L’impression 3D permet la fabrication de ce type de pièce, difficile à produire, d’un seul tenant, et sans perte de matière.
- L’industrie automobile est un domaine qui fabrique en très grande série. L’impression additive a été largement adoptée, que ce soit pour le prototypage de pièces mécaniques, la fabrication de pièces de protections, ou encore l’impression de pièces de rechange. Permettant ainsi de réduire les coûts d’achats indirects, mais aussi les stocks.
- Le secteur médical investit dans la fabrication additive pour imprimer en 3D des organes à partir de tissus humains. En 2019, une équipe de chercheurs a réussi à imprimer un cœur. Les implants, ou encore des plâtres, sont déjà fabriqués et utilisés à l’heure actuelle. La facilité et la rapidité d’impression font de cette solution un moyen rapide de répondre aux besoins des industriels. Cependant, la production en série reste difficile, car l’impression d’une série ne peut se faire qu’avec intervention entre chaque impression. Et l’impression de grandes pièces peut durer plusieurs jours, à moins de réduire ce temps, au détriment de la qualité d’impression.
Actuellement, l’application la plus répandue à ce jour reste le prototypage. On retrouve ainsi un intérêt tout particulier à imprimer un prototype via l’impression 3D, pour le tester en conditions réelles. Avant de le valider et de le faire fabriquer par usinage.
L'intelligence au coeur de l'industrie du futur
À mesure que l’on apprend de cette technique, les connaissances dans ces matériaux évoluent. Ils permettent ainsi de proposer des produits toujours plus aboutis et complexes.
Autres avantages, un fort gain de flexibilité, la possibilité de créer et de fabriquer des pièces de rechange très rapidement. Mais également réduire les stocks et produire des pièces qui ne sont plus fabriquées.
L'Évolution dans le futur
La composition de ces techniques de fabrication avec l’intelligence artificielle permettra dans le futur d’automatiser ces processus de fabrication. Mais aussi de faire évoluer les produits, pour leur offrir de meilleures propriétés, réduire les temps d’arrêts, faire communiquer les machines entre elles. Afin d’assurer une fabrication sans interruption et sans perte.
L’évolution de ces techniques de fabrication dans d’autres domaines est déjà en marche. Avec l’apparition de la fabrication additive dans la construction de maisons ou la fabrication de moteurs de fusées.
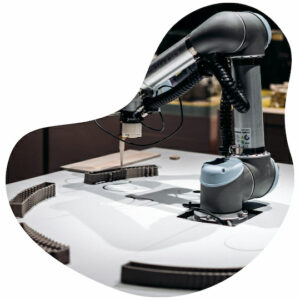
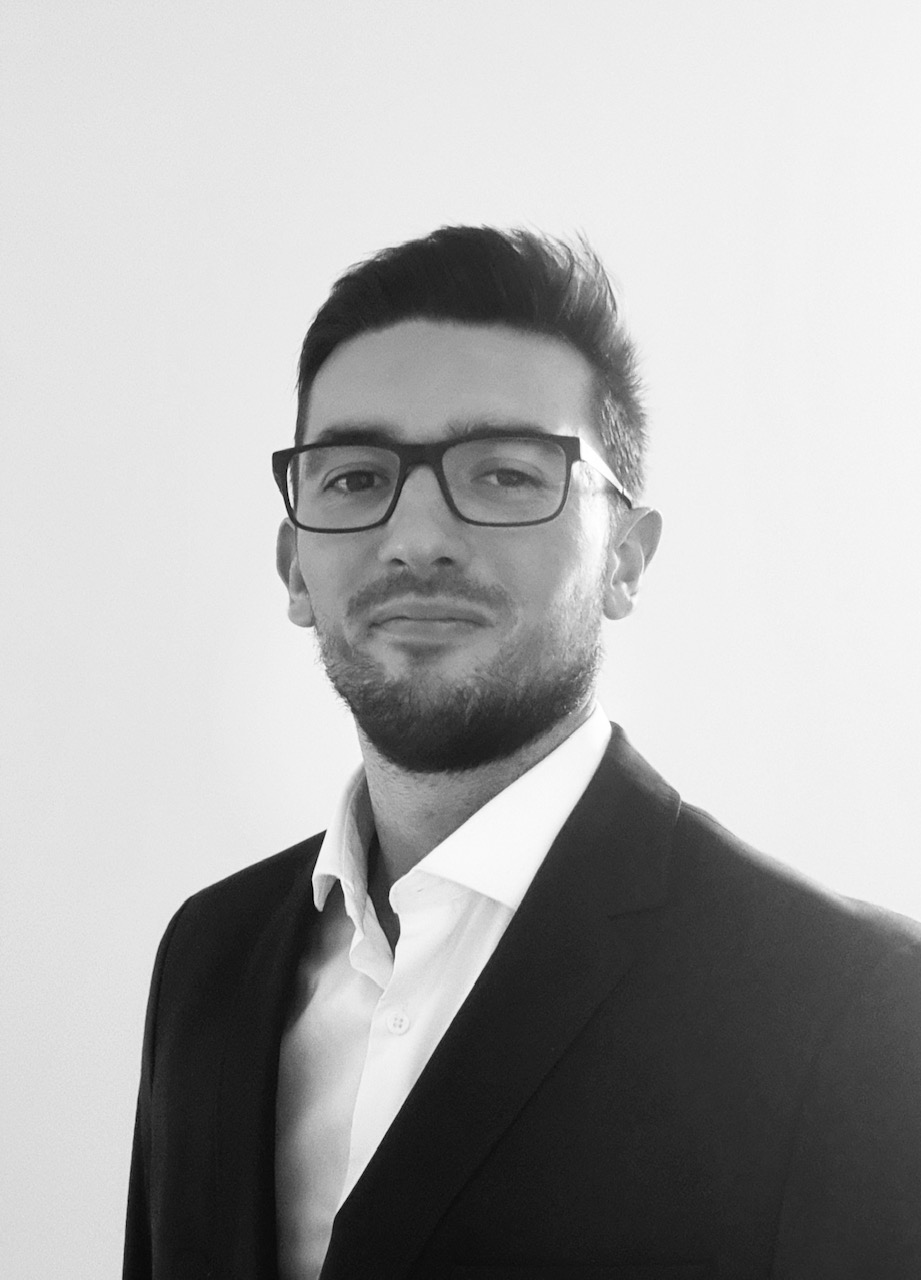